Fight waste of resources with Lean Production
The goal of Lean Production is to eliminate waste in production. Overproduction, inventory, transportation routes, wait times, complicated processes, scrap and downtime cause significant extra costs. Resources in the form of materials, time and labor are wasted. We streamline your production processes with Lean Production and increase the productivity of your facility. Especially in the area of mass production the positive effects of process optimization through Lean Production are especially evident.
Identify cost drivers
Production is the heart of operating value creation. In order to continuously produce at a world class level important cost drivers must be identified. Potential savings can only be revealed with the right methods, which ensure long term maximum performance and competitiveness. As leading international management consultants we know the value of Lean Production:
- avoid mistakes
- eliminate waste
- establish continuous improvement
For us, Lean Production is the elimination of all unnecessary work steps and the significant reduction of processes. This can only be achieved through the highest possible optimization and standardization of all production processes. The greatest possible effect is achieved in Lean Production not in using individual measures but only through the combination of various management approaches to optimize production.
Lean Production tailored
Therefore our experienced management consultants choose the exact approaches from our Operational Excellence Toolbox which are tailored for your situation and company. With personalized Best-of-Best solutions we achieve sustainable results. To achieve these results through Lean Production we tailor our tested methods to your individual requirements. We combine and expand proven methods such as 5S, SMED or TPM with unique innovative concepts developed by our consultants.
Typical results of Lean Production
- Cost reduction through concentration on value creating activities
- Efficiency increase through streamlining of existing processes
- Development of new, efficient production processes
- Reduction in transportation and processing costs
- Quality improvements in processes and products
- Strengthened responsibility of work force
- Establishment of a sustainable culture of improvement
Value creation is the centerpoint
Concentration on the essential in Lean Production means optimum utilization of resources. Core processes and all support processes necessary thereto must be identified and uncoupled from non-value-added activities. Our interdisciplinary consulting teams analyze together with your employees the current state of your production processes and organization. Based on our cross-functional experience we quickly recognize the starting points for necessary changes using Lean Production. However, there are in every company individual requirements, which must be taken into account in the preparation of solutions.
Joint evaluation
Here the experience and close collaboration with your employees is especially important. All results are analyzed, documented and evaluated. They form the basis for the development of improvement plans and optimization scenarios, the impact of which can be evaluated using computer simulations.Using Lean Management all waste of resources should be avoided, for example:
- Using Lean Management all waste of resources should be avoided, for example:
- Overproduction: Inventory costs, unclear sales potential
- Scrap: Loss in sales through quality defects
- High materials on hand, capital commitment, inventory costs
- Transport distances: Long distances increase the possibility of process problems
Synergies through combination of methods
Unsere Konzepte zur Prozessoptimierung betrachten teilweise Einzelaspekte der Lean Production, erzielen aber in Kombination zusätzliche Synergien.
Ungeplante Stillstände, Qualitätsmängel und Leerzeiten beeinträchtigen die Gesamtanlageneffektivität/OEE, Produktivitätssteigerungen können durch gezielte Gegenmaßnahmen erreicht werden.
- Mit unserem Konzept 5S werden Sauberkeit, Ordnung und Disziplin für die Mitarbeiter verbindlich in den Arbeitsalltag integriert. Durch die Stärkung der Eigenverantwortung steigt zudem die Motivation der Mitarbeiter. Verstärkt wird dies durch die Einführung kontinuierlicher Verbesserungsprozesse wie beispielsweise Kaizen oder dem Continous Improvement Cycle.
- Mit Verbesserungen im Anlagen- und Instandhaltungsmanagement durch SMED und/oder TPM können Ausfall- und Rüstzeiten nachhaltig verringert und bei Störungen schnelle Gegenmaßnahmen ergriffen werden.
- Durch die Kombination von Wertstromanalyse und Fabrikplanung können bei der Neuentwicklung oder Reorganisation von Fertigungsprozessen bereits in der Planungsphase schlanke Prozesse entwickelt werden.
- Die Verbindung von Wertstrom und Kanban senkt durch intelligentes Management die Lagerbestände der für die Produktion benötigten Verbrauchsmaterialien sowie die Durchlaufzeiten in der Produktion
Kommunikation unverzichtbar
Entscheidend für den Erfolg von Prozessoptimierungen durch Lean Production ist die frühzeitige Einbeziehung der Führungskräfte und betroffenen Mitarbeiter. Als führende Managementberatung optimieren wir daher nicht nur Ihre Prozesse, sondern entwickeln mit Ihnen eine transparente Kommunikationsstrategie. Denn mit der Verschlankung der Prozesse steigt die Verantwortung des einzelnen Mitarbeiters. Die neuen Arbeitsstrukturen erhöhen meist die Motivation der Mitarbeiter und stellen beispielsweise durch neue Qualitätsmanagementansätze und kontinuierliche Verbesserungsansätze neue Anforderungen an die Unternehmenskultur.Wir unterstützen Sie daher nicht nur bei der Konzeption und Umsetzung der Lean Production, sondern erarbeiten auch gemeinsam mit Ihnen Personalentwicklungskonzepte und Zielvereinbarungssysteme. Unser Ziel ist es, eine lernende Organisation aufzubauen, in der das Wissen und Können aller Mitarbeiter berücksichtigt und die Unternehmenskultur kontinuierlich weiterentwickelt wird, um Lean Production dauerhaft im Unternehmen zu verankern. Bei Bedarf führen wir auch Schulungen oder Coachings für Ihre Mitarbeiter durch.
Erfolgsfaktoren für Lean Production
Um das Prinzip Ressourcenverschwendung zu vermeiden und konsequent zu leben, sollten folgende Aspekte in einem ganzheitlichen Lean Production-Konzept berücksichtigt werden:
- Anlagentechnik: Die Fertigungstechnik sollte robust und wenig störanfällig sein. Geringe Stillstände durch optimierte Rüstzeiten, eine auf den Materialfluss ausgerichtete Fertigungsplanung und eine intelligente Produktionssteuerung bieten hohe Prozesssicherheit.
- Arbeitsorganisation: Flexibler Einsatz der Mitarbeiter in festgelegten Arbeitsgruppen und flache Hierarchien erhöhen die Motivation und Verantwortlichkeit des Einzelnen. Job-Rotation, die Konzentration auf wertschöpfende Tätigkeiten und eine offene Fehlerkultur stärken die Gemeinschaft und erhöhen die Produktivität.
- Qualitätsmanagement: Ausschuss, Qualitätsmängel, Produktionsausfall durch mangelhafte Instandhaltung wirken sich negativ auf das Gesamtergebnis aus. Standardisierte Prozesse und Routinen zur Qualitätssicherung und Fehlerkontrolle dienen einer reibungslosen Fertigung. Konsequentes Fehlermanagement mit direkter Ursachenforschung und soweit möglich Fehlerbehebung stabilisieren die Prozesse zusätzlich.
- Kontinuierliche Verbesserung: Erfolgreiches Qualitätsmanagement orientiert sich an dem Prinzip „Wir wollen besser werden – ohne Kompromisse“. Dies ist nur in einem Umfeld möglich, in dem Fehler als Chance für Veränderung gesehen und Verbesserungsvorschläge, egal aus welcher Hierarchieebene, ernst genommen werden. Die Mitarbeiter sind die Experten. Diese Sichtweise erfordert häufig eine nachhaltige Veränderung der Unternehmenskultur.
- Mitarbeiter: Spitzenleistung ist nur mit qualifizierten und motivierten Mitarbeitern erreichbar. Die frühzeitige Einbeziehung der Mitarbeiter in Veränderungsprozesse erhöht deren Akzeptanz. Neue Arbeitsorganisation mit klaren Zuständigkeiten und Verantwortlichkeiten sowie gezielte Qualifizierungsmaßnahmen senken die Fehleranfälligkeit und erhöhen die Arbeitszufriedenheit.
- Verfügbarkeit: Alle benötigten Produktionsmaterialien müssen in ausreichender Menge und Qualität zum richtigen Zeitpunkt zur Verfügung stehen. Gleichzeitig sollen Lagerbestände und Transportwege auf ein Minimum beschränkt werden. Hierzu sind intelligente und flexible Versorgungs- und Lagerkonzepte notwendig.
- Prozessorientierung: Der Produktionsprozess soll fließen und sich ausschließlich auf die Wertschöpfung fokussieren. Das erfordert, alle Prozesse auf ihren wertschöpfenden Anteil hin zu überprüfen und von Prozessen ohne Wertschöpfung abzukoppeln. Prozessorientierung ergibt sich dabei aus der konsequenten Optimierung der vorgenannten Faktoren der Lean Produktion.
Dynamische Prozesse nutzen
Mit der Umsetzung der Maßnahmen sollte, soweit möglich, umgehend begonnen werden, um die Dynamik des Prozesses ohne Zeit- und Motivationsverlust zu nutzen und durch die optimierten Prozesse schnelle Ergebnisse in der Lean Production zu erzielen. Als erfahrene Managementberatung unterstützen wir Sie in der Pilotierung und Einführung der vereinbarten Maßnahmen sowie die Trainings- oder Coaching-Maßnahmen für Ihre Mitarbeiter.
Unser Engagement für Ihre Ziele
TARGUS wächst seit unserer Gründung vor 11 Jahren kontinuierlich. Mit großer Motivation setzen wir uns an unseren Standorten in Ratingen und Detroit und natürlich vor Ort in Ihrem Unternehmen für Ihre Ziele ein. Dabei stellen wir hohe Anforderungen an unsere Arbeit und Ergebnisse. Unsere Kunden wissen das und schätzen
- unsere Erfahrung und unseren technischen Sachverstand
- die Zusammenarbeit auf Augenhöhe
- unsere systematische und transparente Arbeitsweise
- das maßgeschneiderte Projektvorgehen
- unsere herausragenden Ergebnisse
- availability of our consulting teams for advice after the project is over.
Vertrauen Sie unserer Kompetenz, Erfahrung und Arbeitsweise. Wir helfen unseren Kunden aus Handel und Industrie, wo immer es erforderlich ist – an Ihrem Stammsitz oder in den Niederlassungen, national oder weltweit. Die Ergebnisse geben uns Recht. Erreichen Sie gemeinsam mit TARGUS Spitzenleistungen.
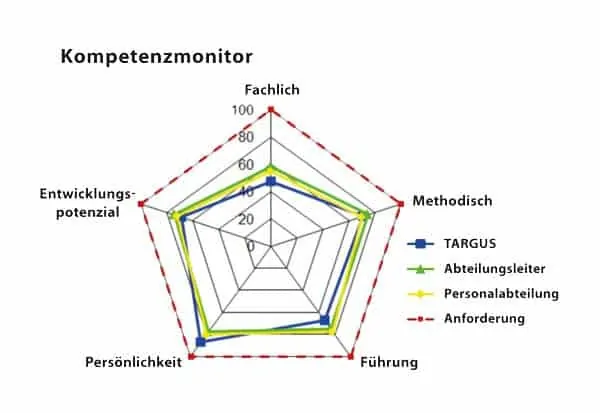
Mitarbeiterverbesserung tailored
Mit unserem Modul Teamleader Improvement Program (TIP) legen wir für fünf Kategorien messbare Evaluierungskriterien fest. So können wir Leistungsstand und Kompetenz der Mitarbeiter im Vergleich zu den neu definierten Erwartungen des Top-Managements ermitteln. Anhand des Kompetenzabgleichs werden individuelle Entwicklungspläne und Coaching-Maßnahmen für die Mitarbeiter entwickelt. Anforderungsprofil und individueller Erfüllungsgrad werden vor den Trainings für jede Führungskraft messbar dargestellt. Nach den Trainings wird erneut bewertet und die Leistungsverbesserung transparent gemacht. So erreichen wir eine rasche Leistungsentfaltung der einzelnen Führungskräfte und tragen entscheidend zur Mobilisierung Ihrer Organisation bei.
Typische Ergebnisse der Mitarbeiterverbesserung
- Stärkung der Eigenverantwortung der Mitarbeiter
- Erhöhung der fachlichen Kompetenz der Mitarbeiter
- Steigerung der Motivation
- Bessere Kommunikation zwischen Führungskraft und Mitarbeiter
- Coaching
Mitarbeiterverbesserung in der Praxis
Um die fachlichen und persönlichen Kompetenzen der Schichtführer einer Schmiede zu stärken, setzten wir in Ergänzung eines OEE-Projektes unser Teamleader Improvement Program (TIP) zur Mitarbeiterverbesserung ein. In Mitarbeitergesprächen wurden gemeinsam mit den Personalverantwortlichen und den Linienvorgesetzten die Erfahrungen und Entwicklungspotenziale der Schichtleiter bewertet.
Anhand der persönlichen Kompetenz- und Anforderungsprofile wurde ein individuelles Coaching-Konzept mit messbaren Kriterien entwickelt, das in das Tagesgeschäft integriert wurde. Das Projekt zur Mitarbeiterverbesserung fand nicht nur eine breite Akzeptanz, sondern erzielte auch eine hohe Aufmerksamkeit innerhalb der Organisation. So erweiterten alle beteiligten Schichtführer ihre Kompetenzen und zeichnen sich durch deutlich mehr Eigenständigkeit aus.