Factory planning begins with an analysis
Through analysis of the individual processes we reveal manufacturing steps and value streams in order to recognize weaknesses and bottlenecks. Using simulation our logistics experts can not only display the comparison between internal and external performance, but prepare effective suggestions for your plant design.
Correct factory planning increases productivity
The construction or redesign of new plants and manufacturing facilities is especially demanding but also offers significant optimization potential. Even minor layout changes can measurably decrease throughput and significantly increase productivity. Based on their personal production experience our OpEx experts develop practical solutions for your factory planning and optimization processes.
Tailored factory planning
Each factory is unique. Therefore we tailor the individual steps on-site to your desires and specifications.
- Record and analyze critical processes and procedures
- Prepare a computer supported model for the entire process
- Simulation of different parameters (i.e. different plant layouts, equipment, loading, workforce capacities)
In the simulation phase, key aspects can be flexibly altered and their effect assessed. Thus we develop with you the most effective measures for your factory.
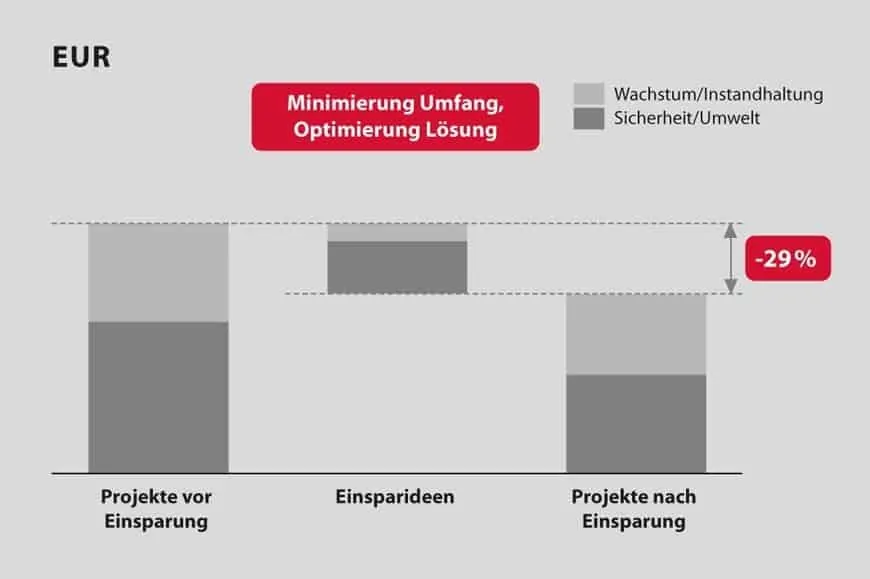
Typical results of factory planning
- Transparency of manufacturing processes, bottlenecks and optimization possibilities
- Identification of non-valued-added activities
- Cost savings of 10-20%
- Reduction of throughput times by up to 50%
Factory planning in action
A German shipyard had to decide whether to bring the manufacture of a steel hull in house or outsource it. Our management consultants were commissioned to study both options in detail and prepare suggestions to optimize internal production.
First, approximately 2000 individual processes for steel processing were analyzed and combined in a simulation with work times, resources and throughput times. Factory planning and optimization suggestions were discussed with the production team and their effects on costs and through times were simulated.
To maintain their internal workforce the shipyard decided to manufacture in house and implemented the 10 most effective improvement measures, saving 20% of the man-hours to produce the steel. In a further step, the Targus experts analyzed the pipefitter shop using the successful factory planning concept and achieved a cost reduction of 25% and a reduction of throughput times of almost 50%.